A packed out event , taking BIM to the next level !
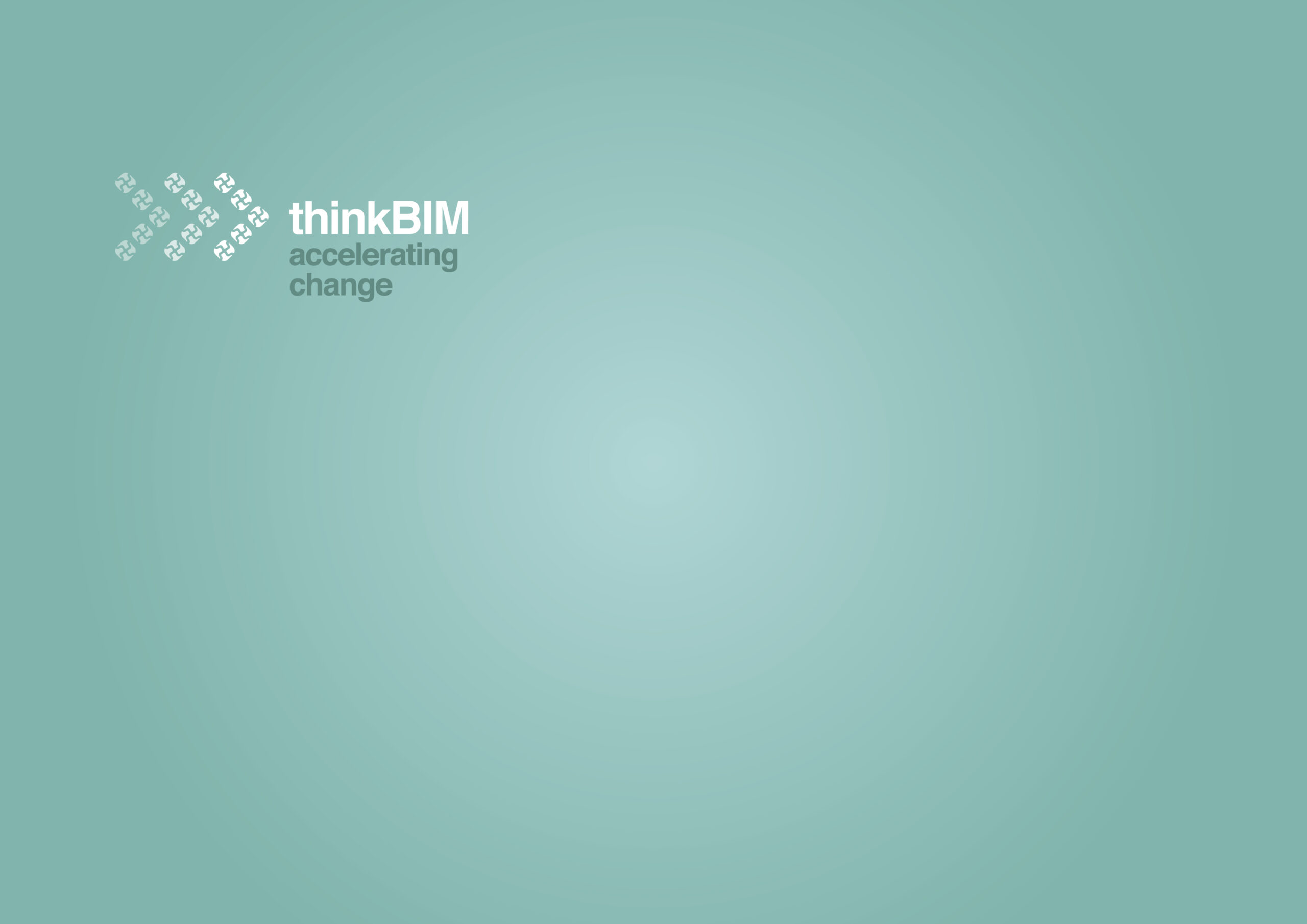
Over 50 construction professionals including contractors, consultants, architects, engineers academics and students filled the lecture theatre in the Rose Bowl in Leeds last week for what was a great start to our thinkBIM’s spring BIM: Construction and Assembly series.
Members of The BIM Academy Build Qatar Live Competition Winning team shared their experience and lessons learnt from the intensive 48hr competition, testing multi-disciplinary collaborative BIM to the maximum in a very high pressure environment, utilising up to 30 different softwares (some of which I have highlighted below).
Founder of the Build Live competitions and COO of Asite, Nathan Doughty, opened and chaired the evening stressing the BIM Academy teams’ excellence in organization and delivery due to their existing working relationships, a set of common goals and an appetite to test a variety of BIM tools.
Peter Barker kick-started the presentations with 3 key critical success factors for them as a team: Rigorous forward planning ; team working with clear lines of responsibility and good communication .George Mokhtar, senior BIM Coordinator for BIM Academy gave an impressive account of their 48hr experience and their winning performance with detailed information on costing presented by Dave Monswhite cost manager for Turner and Townsend , architectural design by Jonnie Flavin, Ryder Architecture, model validation process and COBie information by Michael Serginson, BIM Academy and Dave Fuller from NBS providing specification information.
George opened the evening taking our group through the Build Qatar Live pre-planning and set up of the team that was undertaken, stating and stressing the importance of initial clarity of team roles, BIM uses, Modelling standards, formats of information exchange and programming in 20 min chunks. Jonnie provided an insight into the design process and how the team responded to the brief with thoughts on spatial issues, context (including views out back to Doha), adjacency as well as historical aspects. Lots of early on debate on massing and scale with sketches and diagrams coming thick and fast, working with Felt tip pens and BIM concurrently.
George referred to the three stages of the project as Mass Model, Design Model and the Model Federation for which the co-location was key as scope for misunderstanding information was minimized in a shared space. The real time mass model, allowed instant scheduling of floor areas and gave consultants confidence of the concept going forwards.
Work in Progress (WIP) models from the design team were uploaded to Asite as IFC. These were downloaded and opened in Solibri Model Checker to be validated. Various aspects checked including space properties, overlapping intersections and duplications. Relevant information was highlighted and reported back via Asite with comments and actions. This allowed the team to review the models for any major clashes and discrepancies within approximately 30 minutes, improved collaboration and reduced the potential for iterative design further on in the project. The model validation also provided the cost management team with an accurate model, allowing for greater cost precision at an earlier stage in the project.
Dave Monswhite described the project as ‘like a freight train’ with sub groups having to work in parallel to achieve the outcomes required in the tight time frame. 4D was implemented linking the project construction programme through to Navisworks, allowing the to create construction simulations highlighting any issues with site logistics. The model was being used to inform the cost plan , this was done open source linking validated IFC data into COSTx software, using Qatari cost data. He highlighted the use of individual parts of the federated model to allow different disciplines of building to be taken off at the same time without a clash ‘Quantum is quantum’. For him, quantity wise there is no need to use federated model in these circumstances.
George indicated up to 30 different types of software used throughout the process, indicating the use of Tekla BIMSight as a ‘sanity check’ for clash detection as they progressed. iCIM, the Interoperable Carbon Information Model (iCIM) TSB research project into BIM and financial and environmental cost information gave the capabilities of changing specification and monitoring differing Carbon levels via a carbon monitor on the screen. He also indicated a open source pedestrian modeling tool ‘Steps’ an agent-based micro-simulation tool developed by Mott MacDonald for the simulation of pedestrian movement under both normal and emergency conditions.
Dave Fuller took us through the performance outline and detailed specification work through out the project stressing that the specifications were created as exports from the model, using NBS Create to automatically generate the spec from the model. He described three levels of specification that were developed through the scheme and spoke about how the first version gave a level of detail comparable to the overall model and then subsequent further information was added as the level of detail of the overall model geometry was increased.
The initial brief had been issued as an existing site model and project information in the form of COBie. During the competition the teams had to upload COBie drops on Asite. Rather than the normal 5 for a project this was restricted to three for the competition.
George stressed the importance of having 4 disciplines working together, actually incorporating information into the model.
For the logistics planning and 4D simulation Asta power project was used and then linked into Navisworks to highlight pinch points that were identified at set times of construction.
George brought the presentations to a close with a summary of over 100 documents uploaded to Asite throughout the process and the last minute drama of the gas leak at Northumbria University which nearly lead to the team being unable to submit their final submission document on time!
An interesting Q and A followed with questions focusing on actual processes of getting information into COBie spreadsheets, use of IFC and a broad range of softwares to the benefits these types of competitions can bring to industry and academia as a place where boundaries can be pushed and innovation really happens.